Cracking the nut: Food processing automation from Shibaura Machine
Macadamias are famously the world’s toughest nut to crack. Requiring an extraordinary 300 pounds per square inch of pressure, it is unusual to buy these tough nuts without their shells. Happy Nut by Freedom Fresh Australia is among the exceptions. The Australia-based processing company supplies premium macadamias with a bespoke ‘key’ to crack the nut.
Here’s how the business used robotics from Shibaura Machine to automate the picking-and-placing of keys into their macadamia nut packaging.
Freedom Fresh has long supplied its Happy Nut brand with a specially designed metal key. The macadamia nuts are cleverly roasted with a slit sawed into the shell, meaning customers can crack them open easily using the tool provided.
The challenge the business faced was automating the placement of the keys into bags during the filling process. The manual method was cumbersome and inefficient. It involving a worker standing on a ladder for prolonged periods of time and physically placing a key into each bag.
Shifting from manual to automated processing was a no brainer. The manual task was repetitive and posed obvious safety risks — that’s not to mention the monotonous nature of placing up to 20,000 keys into bags each day.
The goal of the automation project was clear: create a system that would both crack the problem of manual labour inefficiency and improve safety. The requirements included automatic pick and place of up to 60 keys per minute, seamless integration with the existing production line and a minimal factory floor footprint.
Solutions from Shibaura Machine
To meet the requirements, the Freedom Fresh team enlisted automation experts, M.A.P Services , the authorised Australian distribution partner of TM Robotics and Shibaura Machine industrial robots.
The M.A.P Services team selected the THE400 robot as the foundation for the system. The THE series is a flagship SCARA robot range from Shibaura Machine — formerly known as Toshiba Machine until a corporate name change in 2020. The THE series is among the latest robotic launches from the Japanese manufacturer and an ideal choice for pick-and-place applications.
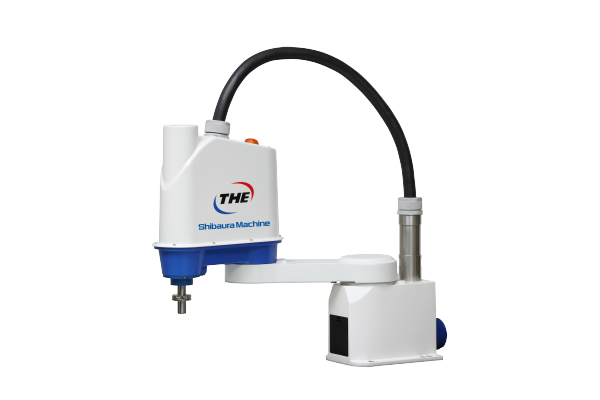
“The THE400 met all of the requirements for the Freedom Fresh project,” explained Nigel Smith , managing director and CEO of TM Robotics. “With a 400 mm arm length, the robot is relatively compact and requires minimal factory floor space. It boasts an impressive cycle time of 0.39 seconds with a 2 kg load and accurate movement trajectory with high-speed operation.”
The robot was equipped with the TS5000, a high-speed, precise robotic controller from Shibaura Machine. M.A.P also integrated an IFM O2D camera for vision processing and an IFM encoder for conveyor tracking, with SMC vacuum gear handling the pick-and-place mechanism.
An automated pick-and-place process
With this equipment now installed, the automated process begins with the IFM O2D camera monitoring a continuous stream of keys on the conveyor. Upon triggering, the camera captures an image and uses its in-built contour detection to locate each key. The camera then sends the position of each key to the robot controller via TCP/IP Ethernet communications.
“Integrating the vision system and encoder with the new generation TS5000 controller presented some initial teething issues,” explained Smith. “However, the user-friendly interface of the controller and the Shibaura Machine robot teach pendant made the integration process significantly easier. Our robot experts worked collaboratively with M.A.P Services to ensure seamless integration.”
The robot syncs with the IFM encoder for accurate conveyor tracking, picks up the key with a suction cup and carries it to the drop point. There, it waits for a signal from the nut-filling machine before releasing the key. This cycle repeats every second, ensuring a high-speed operation that leaves no room for error or delay.
Installation and results
The project exceeded all expectations. The automated system exceeded the cycle time requirement, achieving higher efficiency and reliability. In fact, Freedom Fresh Australia expressed immense satisfaction with the solution.
“Our experience with the new system has been an eleven out of ten,” explained Trevor Steinhardt of Freedom Fresh Australia. “The job of placing keys into bags was a difficult one, and there was no mechanical solution we could find. Now, the system just runs. It is coping very nicely and the strike rate is far better than a human operator.”
Joel Spiteri , the engineer from M.A.P Services that installed and commission the system added, “The first robot installation took place in July 2023, and it has performed flawlessly ever since. What’s more, the impressive results led Freedom Fresh Australia to order three more identical systems. Two of these robots are designed to work in tandem, further increasing cycle times and productivity. The additional robots were installed in early 2024 and are currently in the final stages of commissioning.”
When detailing the success of the project, Spiteri cited several factors. “First, the advanced technology of the Shibaura Machine SCOL, combined with the precision of the IFM O2D camera and encoder, which ensures accurate and rapid key placement. Second, the seamless integration of the THE400 SCARA robot with the conveyor tracking system and vision system to facilitate smooth operation.”
The collaboration between TM Robotics and M.A.P Services was also noted as instrumental to the project’s success. Throughout the design, installation and commissioning stages, M.A.P Services and TM Robotics maintained a collaborative approach. Regular online meetings facilitated effective communication and problem-solving.
“Lastly, it was the customer-centric approach that delivered outstanding results,” added Spiteri. “We ensured that we understand and addressed the specific needs of Freedom Fresh Australia. This effort led to a tailored solution that has exceeded the customer’s expectations.”
Future prospects
Encouraged by the success of this project, Freedom Fresh Australia plans to further explore automation opportunities in its production processes. While automating processes like this one can be a tough nut to crack, leaning on the local expertise of M.A.P Services and the support of Shibaura Machine distributor, TM Robotics, for robot consultation can be the ‘key’ to achieving success.