Luxury packaging plays a critical role in delivering a consumer touch-point experience. However, all mass-produced packaging that serves a functional handling and storage purpose should be given equal attention.
For many consumable products across the value chain, minimalist polymer packaging that delivers a protective shield to safeguard against waste can help to enhance the non-verbal message of sustainability. Symbolically, if packaging items are also processed in the most energy efficient way with less machine downtime, close to zero rejects, and where feasible using recyclable polymers, this unquestionably strengthens the whole lifecycle narrative.
The on-going innovations happening in injection moulding are indicative of just how much sustainable value is aligned to current and future packaging trends and the interlinked dependencies on system efficiencies. With non-recyclable packaging set to be banned by the EU by 2030, UK packaging expert and regional sales manager Ashlee Gough explains why Sumitomo (SHI) Demag is intentionally focusing its efforts on supporting fast-cycling packaging manufacturers to more than halve energy consumption.
Manufacturing packaging has always been about balancing processing speed with cost. Now, the sector is also tasked with reducing environmental impact. With many high-end customers pushing to shift to an all-electric production model, Sumitomo (SHI) Demag has invested a lot of time and energy in creating a machinery collection that fuses the company’s all-electric drive technology, processing speed and energy-enhancing features.
“Fluctuating energy costs creates uncertainty. Particularly for packaging manufacturers where energy is the highest and most unpredictable expense. To counteract this, fast processing repeatability and reduced waste, combined with halving energy costs is now deemed imperative,” explains Ashlee.
Switching to all-electric sounds simple enough. Yet, when you have a model that’s been revered for its speed as much as the company’s hybrid packaging El-Exis series, accomplishing this takes time.
Processing speed has been the biggest hurdle to overcome.
“The challenge for any company is always going to be bringing a packaging machine to market that produces components just as fast, if not faster, without compromising cycle time, service life or energy use,” adds UK Managing Director Dave Raine.
Maintaining repeatability, speed and precision while simultaneously improving energy efficiency by utilising direct drive technology underpins the Group’s packaging strategy. Until recently, matching the force and speed of hybrid packaging machines was inconceivable. But, with 80,000+ all-electric machines now installed globally, Sumitomo (SHI) Demag has fused all their market expertise with application knowledge to edge ahead and give packaging processors the blend of productivity, reliability, and energy savings.
It is all down to Sumitomo’s in-house direct drive technology, emphasises Ashlee. “As each individual axis has a drive that has been developed specifically for each function, it means that packaging processors can achieve faster cycle time plus energy savings of up to 70 percent when compared to hydraulic machines.”
For the past decade, the El-Exis SP set the benchmark in energy consumption for machines operating a 2 second cycle time. PAC-E matches this speed and achieves the same injection dynamics, yet halves the energy consumption. Also filling a critical gap, the company’s latest IntElect S machine is geared specifically towards plastic processors mass-manufacturing narrow tolerance and thin-walled packaging lids and containers at the fastest speeds.
Both machines have been designed to incorporate future digital product passport technology. “As an active member of the R-Cycle community, being able to offer this interoperable software will go a long way towards supporting plastic traceability and the drive towards larger carbon reductions right across the value chain,” adds Dave Raine.
Around 90 percent of the machines installed annually by Sumitomo (SHI) Demag are now all-electric. The company estimates that a third of these are now used by packaging processors to produce caps, closures, lids and containers used by the consumer, medical and food sectors. “These technological advances opens up the associated benefits of the all-electric moulding machine market to even more packaging applications,” ends Ashlee.
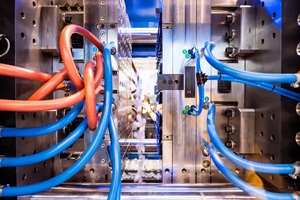
The new PAC-E machine features an all-electric drive, saving packaging processors 50 percent or more in energy when measured against a high-speed hybrid packaging machine
By expanding the IntElect S series, Sumitomo (SHI) Demag opens up the associated benefits of the all-electric moulding machine market to even more thin-walled packaging applications
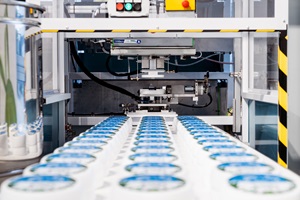
0 Comments