50 years and more supporting UK polymer growth
As Sumitomo (SHI) Demag celebrates 50 years of market presence in the UK and Ireland, the team examine the most important chapters that have helped to shape the industry as we now know it. Including the company launches and events that align to the most important engineering and manufacturing eras in modern history.
Having turned 50 in September, Dave Raine, Nigel Flowers and the team reflect on some of their favourite company moments, encapsulating them into 5 distinctive eras. Including revealing the number one topic flagged at the company’s very first Board Meeting hosted by MD Barry Taylor in Leighton Buzzard on 2nd October, 1974. And why, thanks to Service 3000, digitalisation is anything but a new concept at the forward thinking company
The Heritage Era
Demag Hamilton was formed at the end of September 1974 when Hamilton Machinery combined with Demag AG. At that time, the total market of British built and imported machines was 2,700. There are now over 5,800 companies in the UK plastics industry, operating almost 16,000 machines and contributing £25 billion annually to our economy.
But the history of company in fact predates 1974. Several decades before establishing its presence in the UK and Ireland, Demag had already made a name for itself as an innovator on the continent. Responding to high demand for inexpensive, mass-produced plastic products after the war, Demag Plastics Group (Ankerwerk Nürnberg) manufactured the world’s first reciprocating screw injection moulding machine. This was in the 1950s. A time when manufacturers in all sectors switched from producing metal components to plastic components.
In 1956, Ankerwerk then engineered the world’s first single-screw injection moulding machine, giving more precise control over the speed of injection and enabling materials to be mixed before injection. As agents of Ankerwerk and trading as Hamilton Machinery Sales, the UK company’s first machine was this very machine. And it was installed by British Geon (now BP) of South Wales in 1957.
One year before launching Demag Hamilton, the team in Germany launched the first injection moulding machine employing a digital hydraulic system. It resulted in faster set ups and greater consistency and processing precision over periods of time. “This technology was very much the precursor to the drives we see today. The main difference is the relative efficiency – including energy consumption – and the high repeatability of a digital system. From those very early days (and even before as the UK agent), we’ve been at the forefront of addressing production challenges, whether it’s fast cycling, new technologies or energy consumption,” notes Director Nigel Flowers.
The minutes of those early meetings show that despite 50 years passing – the same market challenges endure. In that first board report, uncovered in the archives, MD Barry Taylor “expressed concern at the continued uncertainty over the UK market.”
In 2012, the company rebranded as Sumitomo (SHI) Demag.
The Support Era
Back in the early days, there were no mobiles, pagers or computers. Nigel’s first job as a service engineer in 1986 involved travelling in the company Ford Sierra 1.6L Estate to IMED in Letterkenny Ireland to fit a number of machines with robot interfaces. “It was January, West Coast of Ireland and bit grim weather-wise. On the plus side I had 15p-a-day luncheon vouchers!”
Articles published by PRW reveals that in 1974 Demag Hamilton employed 10 service engineers with a charge out rate of £3.50 p/h. You may balk, but that was 50p lower than the hourly charge recommended by the PMDA. A responsive service was as important then as it is now, and the company was managing more than 800 Ankerwerk and Stubbe machines – many of which were built in the company’s factory in Craigavon Northern Ireland.
Testament to the longevity of a well-serviced machine, SDUK recently discovered that the Athlone Technology Institute is home to one of the original Craigavon machines. There are murmurings that this slice of manufacturing history will soon be relocated to the Limerick facility. Dave hopes to invite every customer that has used this machine over the years for training to view it in its new location.
Service has always been a critical company differentiator. The UK team was the first to introduce annual machine “check-ups” in 1996. The D-Check evolved into the ErgoCheck, which is now accompanied by activeCare.
A standardised test, the D-Check helped customers ensure their machine was still operating in accordance with the original manufacturer’s protocols and design performance. It later developed into activeCare, where we offered enhanced value to customers by not only checking performance but also changing wear components.
Fifty years on and we are fully immersed in the era of datasets and remote diagnostics. Technical Manager Nick Stockton, who joined the company as an apprentice in 1999, reflects on how important modern connectivity is now for processors and why digitalisation is anything but new.
Sumitomo (SHI) Demag has been building digital datasets for over 25 years. It just didn’t go by the same name. Service 3000 was introduced in 1996 to investigate service pinch points. It generated monthly data reports. So not really real-time. But nonetheless, it was an extremely valuable piece of research to support decision making
“The benefits of digital technologies and dashboards that are now deployed today are incomparable to the days of trying to decipher processing issues when an engineer is calling from a phone box on the road, without being able to see what was happening on the machine,” comments Nick.
The Debut Era
As pioneers of all-electric injection moulding machines and driven by the emerging sustainability agenda, the first SE series was unveiled the same year that Sinead O’Connor’s Nothing Compares 2 U topped the Billboard charts. Towards the end of the decade, fast cycling became a reality with the introduction of modular drive technology on a hybrid El-Exis S high-speed machine.
Setting another trend, the IntElect with water-cooled direct drives for all movement axes launched in 2003. This was designed to meet very specific clean room requirements commonplace in the medical sector. “This represented a move into direct drive, all-electric presses, which until then had mostly been confined to Japan,” observes Nigel
But it was the debut of the DEMAG Ergotech EXTRA machine, also in 2003, that really rocked the market recalls current Managing Director Dave Raine. “This was, by far, our fastest selling and most popular German built machine. For £23,500, processors could get all the additional productivity-enhancing and reliability features that would have usually cost them more. It was a step change in the company’s R&D to ensure that productivity features were no longer a nice-to-have.”
This year, the company launched an IntElect equivalent to the EXTRA. Giving customers a fast-delivery, energy efficient and fast cycling model, without the need for customised features, SDUK recently sold its first IntElect EXTRA to a customer in Ireland.
The Ireland Era
Craigavon can be defined as one of the company’s biggest success stories. In 1974, PRW reported that since starting production of the Stubbe machines in 1967, the production space more than doubled. In seven years, 800 Stubbe injection moulding machines were delivered to customers in Britain and Eire, as well as further afield. Christoph Fischer, GM at that time, was awarded an MBE for his services to industry as result of the success of the Craigavon plant.
Being so deeply rooted in Ireland’s plastics processing sector is often underplayed, reports Dave. But with more than 400+ supported precision machines manufacturing billions of medical, biotech, electronic, automotive, engineering and FMCG packaging components yearly, the company last year opened a Centre of Excellence in Limerick. This now provides customers with direct access to IOM3-accredited training, and a dedicated team of experienced technical, service support and processing professionals.
“Given the maturity of the precision processing market in Ireland, our new Ireland office provides us with the opportunity to serve our customers in the best way possible while building upon our physical footprint in the region,” adds Dave.
The Productivity Era
Last decade the buzz words were sustainability and energy efficiency. Now, productivity is the golden ticket and what every processor is seeking to optimise. Having surpassed 85,000 IntElect global installations in 2022, the Group continue to invest in R&D to unlock efficiency improvements, reduce material waste and address labour shortages
“It’s widely considered a ‘given’ that energy efficiency and reduced pollution are the benefits of all-electric injection moulding machines. Especially in today’s eco-conscious manufacturing world. However, beneath the hood of our IntElect machines are a number of velocity and injection power features that, when used correctly and repeatably by moulding operatives, result in faster cycle times and more stable start-ups. Even before any process optimisation steps have been introduced and expert setting knowledge has been imparted,” exclaims the newest team member and Area Sales Manager Ashlee Gough.
Field tests, combined the with 2024 Productivity roadshow, have been instrumental in helping our customers to identify and introduce further process improvements, notes Ashlee. “For productivity to be sustained, marginal gains is the best approach. Every incremental improvement boosts productivity that little bit more. Providing polymer manufacturers with greater capacity to take on new customers and more projects.”
For the entire team, it’s this attention to detail that ensures customers will continue to remain the strongest advocates of Sumitomo (SHI) Demag machines.
Since the early days, the company has changed beyond all recognition. But our enduring values, service approach, and people focus remains as strong today as ever, asserts Nigel. “As we reflect on everything accomplished, I’d like to thank each and every one of our 400 customers spanning the automotive, IT, packaging, electronic, medical and pharmaceutical, building products and leisure industries for sharing this exciting journey with us to greater productivity.”
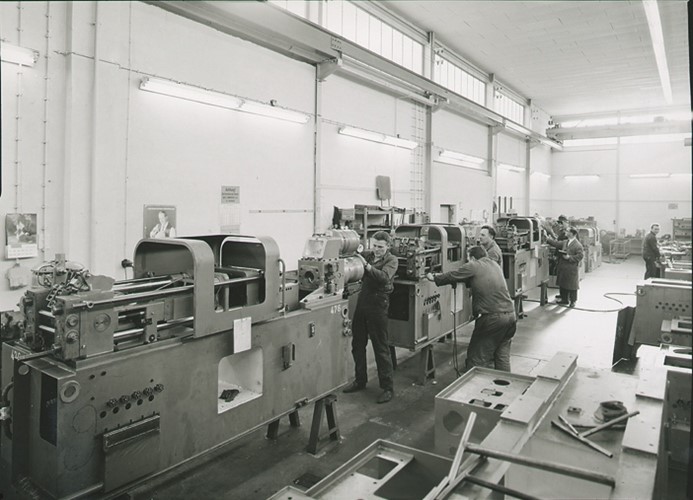
One of the first Ankerwerk machines sold by UK agent Hamilton Machinery Sales was installed by British Geon (now BP) of South Wales in 1957.
These original artworks were commissioned in 1994 to showcase the technological evolution of Demag, which was rebranded Sumitomo (SHI) Demag in 2012.
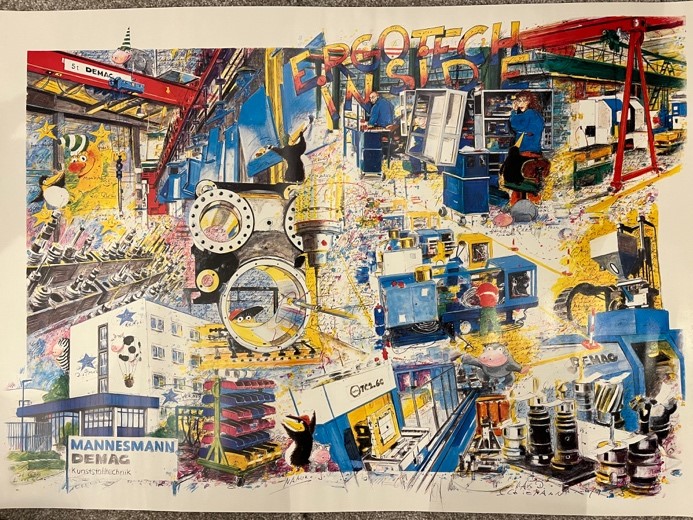
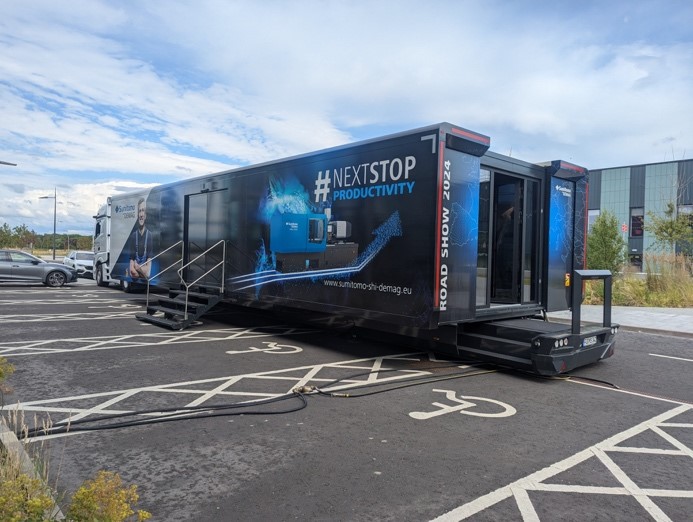
Field tests, combined the with 2024 Productivity roadshow, have been instrumental in helping customers to identify and introduce further process improvements.
SDUK MD Dave Raine (L) and former MD Nigel Flowers (C) were joined by two past Group CEOs Dr Tetsuya Okamura and Gerd Liebig, and former CFO Shaun Dean (R) to look back and mark the significant milestone.
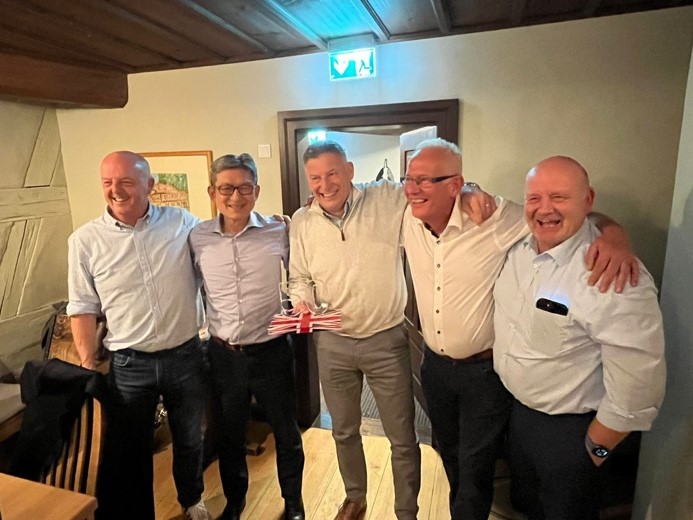
0 Comments